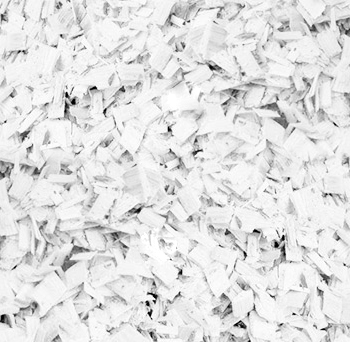
-
220.00 руб. – 295.00 руб.Выбрать ...
- Quick View
Щепа декоративная белая
Щепа декоративная белая
Материал: Щепа хвойных деревьев, Американский краситель, Цвет: Белый
Размер: 2-4 см
Вес: 16-18 кг.
Объем: 1 мешок 60 литров
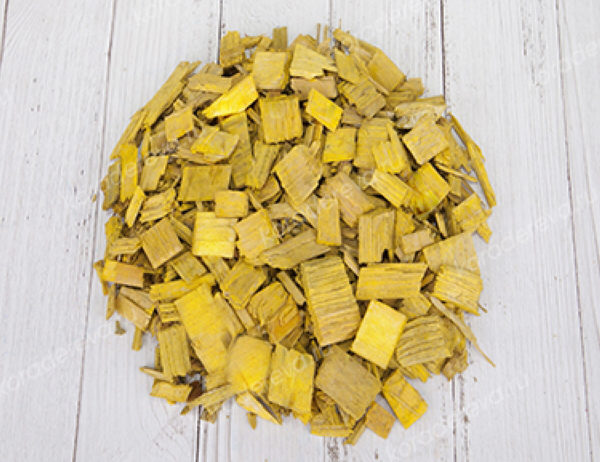
-
220.00 руб. – 295.00 руб.Выбрать ...
- Quick View
Щепа декоративная желтая
Щепа декоративная желтая
Материал: Щепа хвойных деревьев, Американский краситель, Цвет: Желтый
Размер: 2-4 см
Вес: 16-18 кг.
Объем: 1 мешок 60 литров
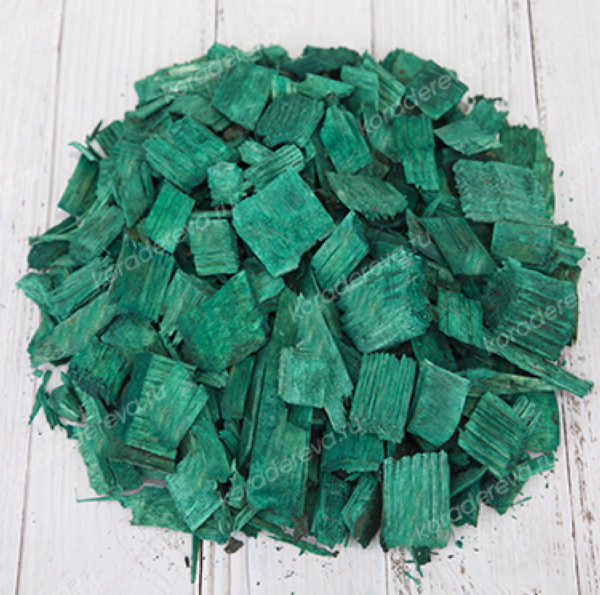
-
220.00 руб. – 295.00 руб.Выбрать ...
- Quick View
Щепа декоративная зеленая
Щепа декоративная зеленая
Материал: Щепа хвойных деревьев, Американский краситель, Цвет: Зеленый
Размер: 2-4 см
Вес: 16-18 кг.
Объем: 1 мешок 60 литров
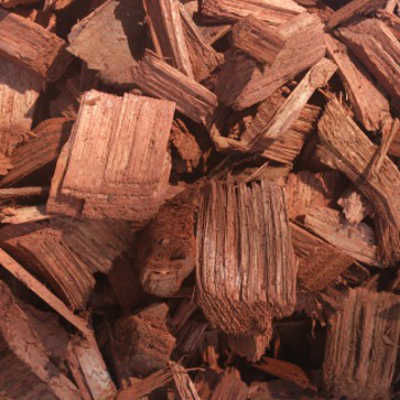
-
220.00 руб. – 295.00 руб.Выбрать ...
- Quick View
Щепа декоративная коричневая
Щепа декоративная коричневая
Материал: Щепа хвойных деревьев, Американский краситель, Цвет: Коричневый
Размер: 2-4 см
Вес: 16-18 кг.
Объем: 1 мешок 60 литров
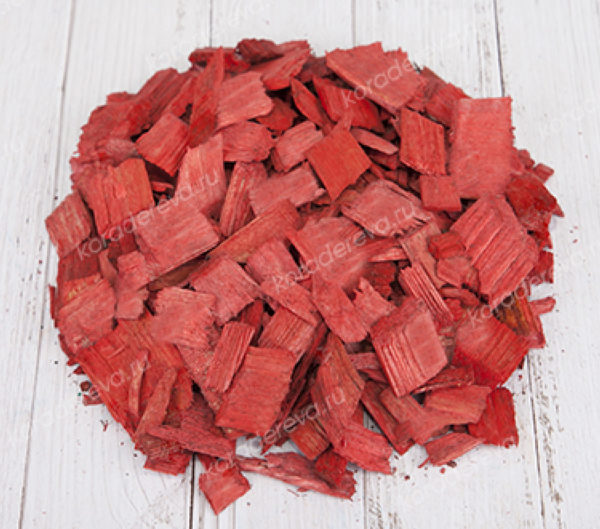
-
220.00 руб. – 295.00 руб.Выбрать ...
- Quick View
Щепа декоративная красная
Щепа декоративная красная
Материал: Щепа хвойных деревьев, Американский краситель, Цвет: Красный
Размер: 2-4 см
Вес: 16-18 кг.
Объем: 1 мешок 60 литров
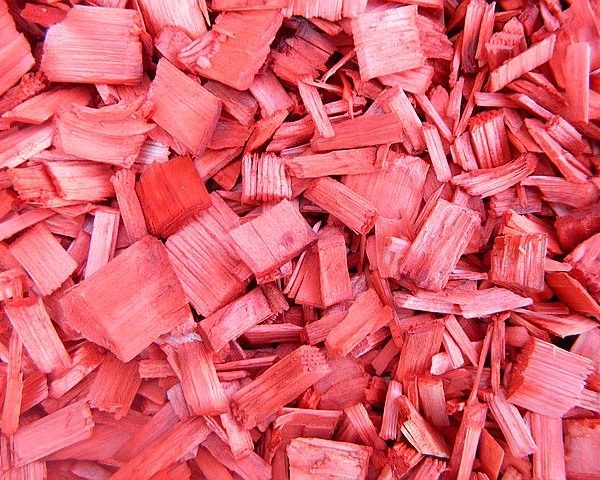
-
220.00 руб. – 295.00 руб.Выбрать ...
- Quick View
Щепа декоративная малиновая
Щепа декоративная малиновая
Материал: Щепа хвойных деревьев, Американский краситель, Цвет: Малиновый
Размер: 2-4 см
Вес: 16-18 кг.
Объем: 1 мешок 60 литров
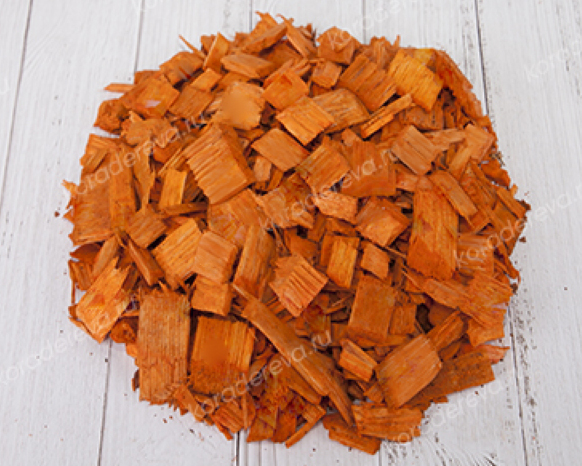
-
220.00 руб. – 295.00 руб.Выбрать ...
- Quick View
Щепа декоративная оранжевая
Щепа декоративная оранжевая
Материал: Щепа хвойных деревьев, Американский краситель, Цвет: Оранжевый
Размер: 2-4 см
Вес: 16-18 кг.
Объем: 1 мешок 60 литров
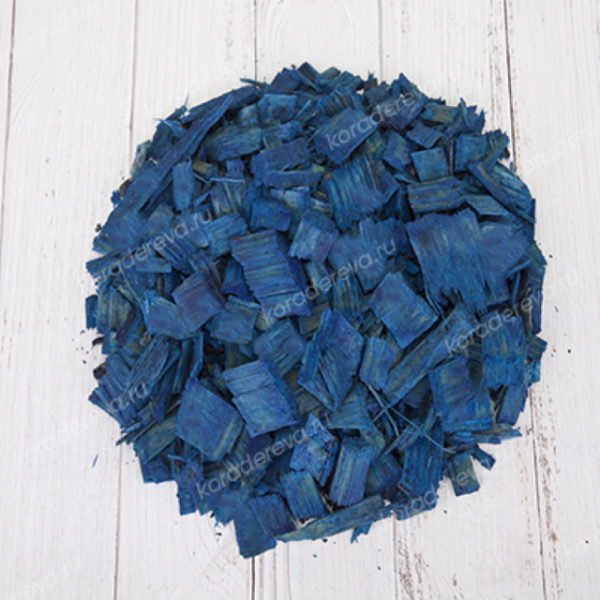
-
220.00 руб. – 295.00 руб.Выбрать ...
- Quick View
Щепа декоративная синяя
Щепа декоративная синяя
Материал: Щепа хвойных деревьев, Американский краситель, Цвет: Синий
Размер: 2-4 см
Вес: 16-18 кг.
Объем: 1 мешок 60 литров
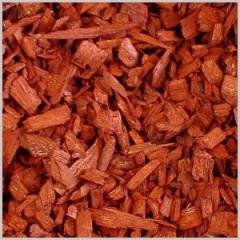
-
220.00 руб. – 295.00 руб.Выбрать ...
- Quick View
Щепа декоративная терракотовая
Щепа декоративная терракотовая
Материал: Щепа хвойных деревьев, Американский краситель, Цвет: Терракотовый
Размер: 2-4 см
Вес: 16-18 кг.
Объем: 1 мешок 60 литров
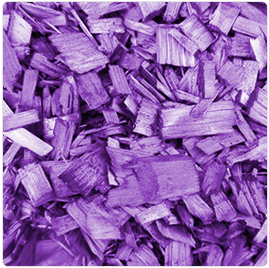
-
220.00 руб. – 295.00 руб.Выбрать ...
- Quick View
Щепа декоративная фиолетовая
Щепа декоративная фиолетовая
Материал: Щепа хвойных деревьев, Американский краситель, Цвет: Фиолетовый
Размер: 2-4 см
Вес: 16-18 кг.
Объем: 1 мешок 60 литров
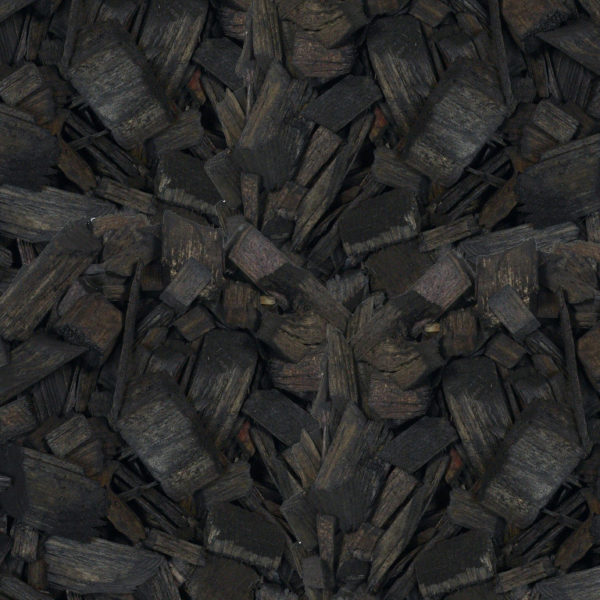
-
220.00 руб. – 295.00 руб.Выбрать ...
- Quick View
Щепа декоративная черная
Щепа декоративная черная
Материал: Щепа хвойных деревьев, Американский краситель, Цвет: Черный
Размер: 2-4 см
Вес: 16-18 кг.
Объем: 1 мешок 60 литров
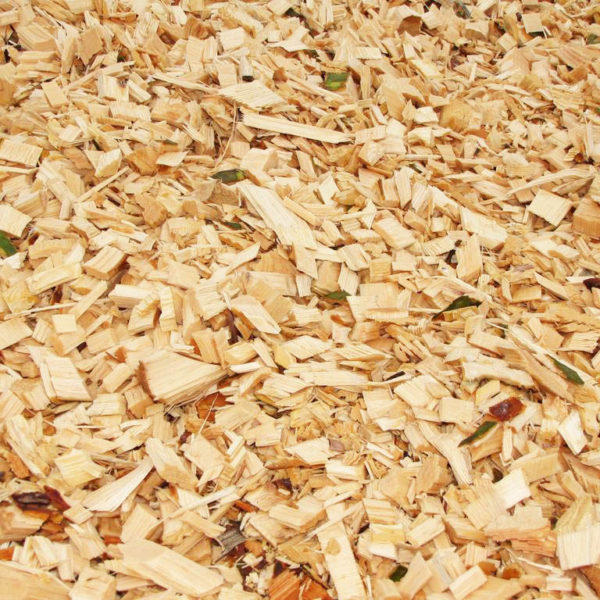
-
170.00 руб. – 260.00 руб.Выбрать ...
- Quick View
Щепа натуральная
Щепа натуральная
Материал: Щепа хвойных деревьев, Американский краситель, Цвет: Натуральный
Размер: 2-4 см
Вес: 13-15 кг.
Объем: 1 мешок 60 литров